I don't do much framing, but I know how important a quality surface is when attaching drywall. This is particularly important when dealing with curved surfaces.
I have been hanging drywall for 26 years now and have attached drywall to some pretty poorly built curves. A few years ago I came in to tape a house that another company had hung, and there were a lot of arches. The carpenter had framed them all out of lumber he cut with a saw. I don't really know how he built them or figured out each radius but it wasn't a very good job. The hangers had just routered out along the framing and attached a strip of drywall to the bottom.
I have always believed that once you start a job you own it, you accept it as satisfactory, and you are then responsible for the quality of the job. So I looked at these arches and decided I was looking at potential trouble.
I decided I had to tear off some drywall on those arches and do some shimming and cutting, and when I attached the beads I really took my time and made little adjustments. While my crew was applying the first coat of tape I worked on the arches. When I was done with the job I had no worries. I had met the customer's expectations. But why did it have to be so difficult?
This reminds me of one of my most common complaints when drywalling a house. When a fiberglass shower unit is installed the flange along the edge of the unit that is attached to the studs sticks out about 1/4 inch. The studs that the shower is attached to should be shimmed so everything ends up nice and smooth and level. A lot of times this isn't done, so when I attach the drywall I can only fasten to the top and along the bottom. I fudge things a little and it looks OK, and then the tile guy comes in and fudges a little by putting in some extra thin-set and cutting the tile a little off square. When the job is done it looks pretty good and the customer is usually satisfied. But if the studs had been shimmed then the customer would definitely be satisfied, I wouldn't have lost time and money, and the same for the tile guy.
I remember a job I did a few years back. It was for a typical customer - they were actively involved in the construction process, they were only somewhat knowledgeable about how everything had to fit together, it was their dream home, and they were quite trusting of us contractors. And oh yes, they were very particular.
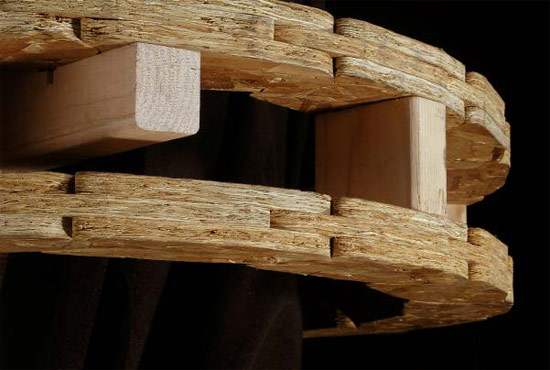
Their front door opened into this large foyer that had a beautiful barreled ceiling. I think the ceiling was framed with USG's Drywall Suspension System. It was very well built and hanging and finishing the drywall was easy. The problem started when I only finished the ceiling to a Level 4 finish. After it was painted and light hit the ceiling from a certain angle, you could see the seams and strips of nails. It was only noticeable at certain times of the day and at certain angles. But it was there. I couldn't tell the customer to just not look up at certain times of the day. The customers' expectations were very high for that ceiling and they expected perfection. The painters had accepted the taping job when they started painted, and now they were the first questioned.
I think the job specs should have called for a Level 5 finish on this ceiling. Because a finish was not specced, I only finished to a Level 4, but I knew it should have had a Level 5. The painters should have known it needed a better finish and could have suggested a primer-surfacer that would have created a Level 5 finish, but they just primed and painted anyway. We all made mistakes, and as you can see, it is easy to blame someone else.
At the SEBC Show
I was recently doing drywall demos at the 2008 Southeast Building Conference in Orlando. Flex-Ability Concepts was one of my sponsors, so I was showing people how to build arches, curved walls and even a barrel ceiling. I don't do much framing, but I know how important a quality surface is when attaching drywall. This is particularly important when dealing with curved surfaces.
When I was done with one of my presentations at the SEBC Show I asked for questions and comments from the audience. A few of the older contractors said they didn't think they would use any of the Flex-Ability Concepts products because they would just use plywood or rip lumber. Maybe they have the skills and even the time to do this. Most of us are looking to make the job simpler and faster to do. It would also be nice if a less skilled person on the crew can do this work.
Jeffrey Grummert, the sales rep in Florida for Flex-Ability products, was at the show so I talked to him about the contractors who use the products. Jeff frequently visits job sites as well as distributors. He said people are using the products for a single arch or up to 100 arches. Once a customer uses a arch or a tract they are hooked. The contractors are looking for curvable framing products that are fast, easy and accurate to work with. The framing contractor is assured a smooth graceful curve and the drywall contractor will not have flat spots or rough spots to fix. The job is done right the first time, with no callbacks. He even stated that using Flex-Ability Concepts products allows your best craftsman to work on other projects.
I also interviewed a company that uses Radius Track Corp. products. I talked to Rubin Turbville, a project foreman for Lasco Acoustics and Drywall Inc. in Dallas, Texas. Rubin said they really like the Radius Track products and that they take advantage of many of the surfaces Radius Track provides. They often take advantage of custom curving and engineering services. The materials come well marked and color-coded for easy assembly. Rubin mentioned the quality of the products a few times. The materials were fast and easy to put together, and the finished job is strong and durable. He said if he had one arch to build, he would prefer to use a manufactured product.
What I learned from giving the demos at the show was that using products, services, and tools made by companies such as Flex-Ability Concepts and Radius Track can add expertise in a segment of the industry that contractors don't deal with everyday. There are ways to accomplish radius framing that significantly alleviate labor/time and reduce costs dramatically. Projects are easier to bid. The drywall crew walks into a job that they are willing to take over and be responsible for. And most importantly the customer's expectations are met. If you don't meet the customer's expectations you may have nobody to blame but yourself.

Myron R. Ferguson is a drywall contactor from Galway, N.Y. He is the author of "Drywall Professional Techniques for Great Results" (recently revised) and has appeared in videos about drywall techniques. He travels throughout the country putting on drywall clinics at trade shows and lumberyards. He also provides hands-on training for companies and technical schools.